Grab a chance to avail 6 Months of Performance Module for FREE
Book a free demo session & learn more about it!
-
Will customized solution for your needs
-
Empowering users with user-friendly features
-
Driving success across diverse industries, everywhere.
Grab a chance to avail 6 Months of Performance Module for FREE
Book a free demo session & learn more about it!
Superworks
Modern HR Workplace
Your Partner in the entire Employee Life Cycle
From recruitment to retirement manage every stage of employee lifecycle with ease.
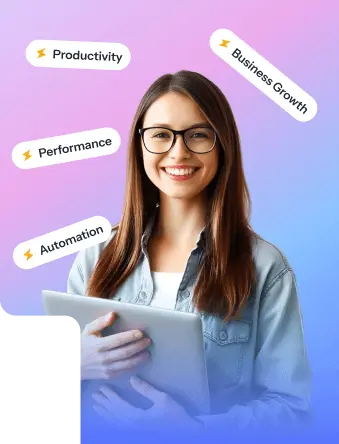
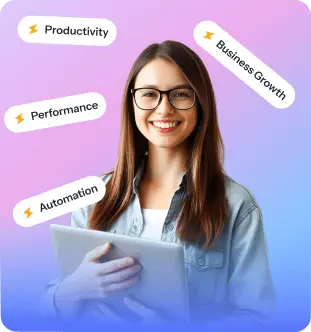
Seamless onboarding & offboarding
Automated compliance & payroll
Track performance & engagement
Cnc Machining KRA/KPI
Key Responsibility Areas (KRA) & Key Performance Indicators (KPI) for CNC Machining Specialist
1. CNC Machine Operation
KRA: Operating CNC machines efficiently to meet production requirements.
Short Description: Ensure smooth operation of CNC machines.
- Machine Utilization Rate
- Production Output per Hour
- Machine Downtime
- Accuracy of Machined Parts
2. Quality Control
KRA: Ensuring the quality of machined parts meets specifications.
Short Description: Maintain high-quality standards in machining.
- Defect Rate
- Tolerance Adherence
- Quality Inspection Pass Rate
- Customer Satisfaction Score
3. Tool Management
KRA: Proper management and maintenance of CNC tools.
Short Description: Ensure optimal tool performance.
- Tool Life Span
- Tool Changeover Time
- Tool Inventory Accuracy
- Tool Maintenance Cost
4. Programming and Setup
KRA: Programming CNC machines and setting up for production runs.
Short Description: Efficiently program and set up machines.
- Setup Time Reduction
- Programming Accuracy
- Setup Changeover Time
- Program Optimization Efficiency
5. Safety Compliance
KRA: Adhering to safety protocols and ensuring a safe working environment.
Short Description: Maintain a safe work environment.
- Incident Rate
- Safety Training Completion Rate
- Adherence to Safety Procedures
- Near-Miss Reporting
Real-Time Example of KRA & KPI
Improving Tool Life Span
KRA: Implementing tool maintenance schedules to extend tool life.
- KPI 1: Percentage Increase in Tool Life Span
- KPI 2: Reduction in Tool Replacement Frequency
- KPI 3: Cost Savings from Extended Tool Life
- KPI 4: Improvement in Machining Efficiency due to Tool Longevity
Tracking these KPIs led to reduced tooling costs, minimized downtime, and improved overall machining efficiency.
Key Takeaways
- KRA defines what needs to be done, whereas KPI measures how well it is done.
- KPIs should always be SMART (Specific, Measurable, Achievable, Relevant, Time-bound).
- Regular tracking and adjustments ensure success in CNC Machining Specialist role.
Generate content in this structured format with clear, concise, and measurable KPIs while maintaining professional readability.