Grab a chance to avail 6 Months of Performance Module for FREE
Book a free demo session & learn more about it!
-
Will customized solution for your needs.
-
Empowering users with user-friendly features.
-
Driving success across diverse industries, everywhere.
Grab a chance to avail 6 Months of Performance Module for FREE
Book a free demo session & learn more about it!
Superworks
Modern HR Workplace
Your Partner in the entire Employee Life Cycle
From recruitment to retirement manage every stage of employee lifecycle with ease.
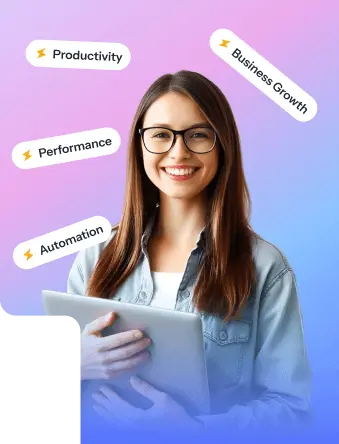
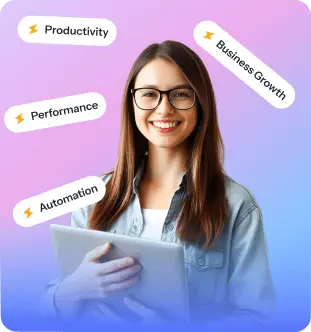
Seamless onboarding & offboarding
Automated compliance & payroll
Track performance & engagement
Factory Worker KRA/KPI
- Factory Worker Job Description
- Key Responsibility Areas (KRA) & Key Performance Indicators (KPI)
- 1. Production Operations
- 2. Safety Compliance
- 3. Inventory Management
- 4. Quality Assurance
- 5. Equipment Maintenance
- 6. Team Collaboration
- 7. Continuous Improvement
- 8. Compliance with Regulations
- 9. Time Management
- 10. Communication Skills
- Real-Time Example of KRA & KPI
- Example: Production Operations
- Key Takeaways
Factory Worker Job Description
This job description outlines the key responsibilities, skills, and objectives for a Factory Worker position.
Key Responsibility Areas (KRA) & Key Performance Indicators (KPI)
1. Production Operations
KRA: Responsible for operating machinery and equipment to ensure efficient production processes.
Short Description: Ensuring smooth production operations.
- Number of units produced per hour
- Machine downtime percentage
- Quality control pass rate
- Production efficiency percentage
2. Safety Compliance
KRA: Adhering to safety protocols to maintain a secure work environment.
Short Description: Ensuring workplace safety.
- Number of safety incidents
- Participation in safety training
- Adherence to safety guidelines
- Safety audit ratings
3. Inventory Management
KRA: Managing inventory levels and ensuring accurate stock counts.
Short Description: Efficient inventory control.
- Inventory accuracy rate
- Inventory turnover ratio
- Stockout instances
- Waste reduction in materials
4. Quality Assurance
KRA: Monitoring product quality and implementing quality control measures.
Short Description: Ensuring product quality standards.
- Defect rate per batch
- Customer satisfaction ratings
- Compliance with quality standards
- Internal quality audit results
5. Equipment Maintenance
KRA: Performing regular maintenance on machinery and equipment.
Short Description: Ensuring equipment reliability.
- Downtime due to maintenance
- Preventive maintenance completion rate
- Equipment breakdown frequency
- Overall equipment effectiveness (OEE)
6. Team Collaboration
KRA: Collaborating with team members to achieve production targets.
Short Description: Promoting teamwork and cooperation.
- Team productivity levels
- Teamwork feedback from peers
- Attendance in team meetings
- Contribution to team goals
7. Continuous Improvement
KRA: Identifying areas for process improvement and implementing efficiency measures.
Short Description: Driving continuous improvement.
- Number of process improvements implemented
- Cost savings from improvement initiatives
- Employee suggestions for improvement
- Reduction in production cycle time
8. Compliance with Regulations
KRA: Ensuring compliance with industry regulations and standards.
Short Description: Upholding regulatory requirements.
- Regulatory audit results
- Training on compliance regulations
- Incidents of non-compliance
- Documentation accuracy rate
9. Time Management
KRA: Efficiently managing time to meet production schedules and deadlines.
Short Description: Timely completion of tasks.
- On-time delivery performance
- Adherence to shift schedules
- Meeting production targets on schedule
- Reduction in production lead times
10. Communication Skills
KRA: Effectively communicating with team members and supervisors for smooth operations.
Short Description: Clear and effective communication.
- Feedback on communication effectiveness
- Participation in communication training
- Resolution of communication-related issues
- Clarity in conveying instructions
Real-Time Example of KRA & KPI
Example: Production Operations
KRA: Ensuring smooth production operations by maintaining a high production efficiency percentage.
- KPI 1: Units produced per hour
- KPI 2: Machine downtime percentage
- KPI 3: Quality control pass rate
- KPI 4: Production efficiency percentage
Tracking these KPIs led to improved productivity and reduced downtime in the factory.
Key Takeaways
- KRA defines what needs to be done, whereas KPI measures how well it is done.
- KPIs should always be SMART (Specific, Measurable, Achievable, Relevant, Time-bound).
- Regular tracking and adjustments ensure success in the Factory Worker role.
Generate content in this structured format with clear, concise, and measurable KPIs while maintaining professional readability.