Facility maintenance software can help teams with predictive maintenance strategies to easily track maintenance schedules, automating routine maintenance & early detection of potential equipment failures. This way, teams can be ensured about reducing the need for expensive emergency repairs & avoid major equipment failures, cutting down overall maintenance costs.
Grab a chance to avail 6 Months of Performance Module for FREE
Book a free demo session & learn more about it!
-
Will customized solution for your needs.
-
Empowering users with user-friendly features.
-
Driving success across diverse industries, everywhere.
Grab a chance to avail 6 Months of Performance Module for FREE
Book a free demo session & learn more about it!
Superworks
Modern HR Workplace
Your Partner in the entire Employee Life Cycle
From recruitment to retirement manage every stage of employee lifecycle with ease.
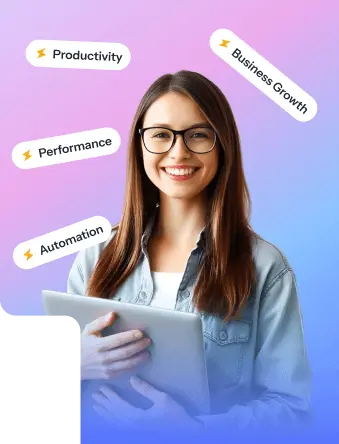
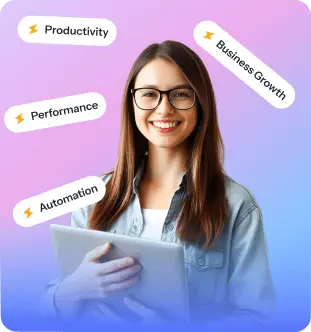
Seamless onboarding & offboarding
Automated compliance & payroll
Track performance & engagement
What Is Facility Maintenance and Why Is It Important for Success?
- facility maintenance system
- 7 min read
- April 15, 2025
For any company in the world, facility maintenance is much more crucial than we think, especially when they have to keep their business operations running as smoothly as possible. This highly needed process maintenance is not limited to just checking building systems; it’s much more than that!
The process further involves scheduled inspections to manage HVAC systems for field teams, ensure fire safety systems are operational, & prevent equipment failures. But why are such facilities maintenance services much required in today’s modern times?
Because those businesses that are overlooking this facility maintenance often end up facing major equipment failures, unexpected emergency repairs & high maintenance costs. And all of these hurdles keep bringing many problems—which can disrupt daily operations.
But why should HR managers and CEOs care about this strategic planning? And the answer to this question is quite simple—a well-maintained facility can experience way more benefits than both HR managers & CEO can think of!
Because companies can easily boost their operational efficiency, ensure compliance with safety standards, and extend the very lifespan of their crucial physical assets with much ease. Moreover, ensuring such facility maintenance management also creates a safe and much more productive work environment, which can easily keep both employees & clients happy.
This blog will cover:
- What is facility maintenance all about?
- How does it reduce downtime?
- Key benefits that businesses can’t ignore!
- Different types of facility maintenance and why they matter!
- How facility management software can simplify operations?
So, dear readers, are you ready to explore how proper maintenance can help you save costs & improve asset performance? Let’s dive in.
What is Facility Maintenance?
Companies managing the facility should all know about the crucial process called facility maintenance. Because this process can bring efficiency to their workflow, by keeping a business’s physical assets, such as commercial buildings, residential buildings, and office buildings, in the best and optimal working condition all the time. This process further includes activities like;
- Building maintenance,
- Managing companies’ very HVAC systems,
- Maintaining their plumbing systems,
- Ensuring electrical systems work efficiently, and
- Monitoring fire safety systems.
But who will be a facility management professional to conduct such inspections, like who would be responsible for this? To answer this question, we would like to mention that in order to prevent equipment failures & reduce equipment downtime, facility maintenance workers and facility managers will be responsible for conducting crucial maintenance activities such as;
- Regular inspections,
Routine maintenance, and - Scheduled maintenance.
Here, the goal is quite simple, to support daily operations seamlessly, and that too without interruptions caused by unexpected breakdowns or safety risks.
What International Facility Management Association have to say about it?
The International Facility Management Association emphasizes is pretty consistent that a facility maintenance plan is not only about fixing things whenever they break. Rather, it keeps involving a well-planned facility maintenance program that continues to address both short-term and long-term maintenance needs. And for that reason, only, a highly efficient facility maintenance system includes;
- Preventive maintenance,
- Predictive maintenance, and
- Corrective maintenance.
Moreover, these modern businesses keep relying heavily on efficient field service software for small business to streamline their entire maintenance operations. Furthermore, such an efficient system can help companies financially as it helps reduce maintenance costs & optimize maintenance schedules.
So, to increase equipment reliability, companies should directly invest in facility maintenance, which quite consistently supports business continuity planning & adheres to health and safety standards. Furthermore, let us help you understand how this property maintenance can enhance operations by subsequently reducing downtime.
How Can Facility Maintenance Reduce Downtime?
This facility & equipment maintenance keeps reducing equipment downtime by preventing all potential equipment failures through both regular inspections & preventive maintenance. And with the help of highly efficient facility management software, businesses unlock the ability to schedule timely repairs, avoiding costly emergency repairs & operational disruptions.
After getting all the basic information about maintenance facility management, now it’s time to learn about all the key benefits!
4 Key Benefits of Facility Maintenance
Just like the HVAC companies who are using HVAC field service software are reaping the benefits of efficiency, so let’s have a look at the benefits that facility professionals are experiencing after ensuring proper facilities and maintenance.
1. Minimizes Equipment Downtime
How can someone minimize downtime in their company? The answer lies in routine maintenance tasks. And among those routine tasks are such as preventive maintenance and scheduled maintenance reduce unexpected equipment failures. Henceforth, once routine maintenance has been ensured, there will be no hurdle in operations consistency in the company.
2. Reduces Maintenance Costs
Once the companies have ensured planned maintenance activities in their workflow, they will face much lower emergency repairs and major equipment failures. And that will help those businesses to save their expensive fixes. So, when a company has efficient facility management software, both tracking and controlling maintenance costs becomes way much easier.
3. Improves Asset Performance and Lifespan
Proper facility maintenance is there to enhance and ensure optimal asset performance and prolong the lifespan of assets such as HVAC systems, plumbing systems & electrical systems. And that directly helps businesses to maximize their returns on capital assets.
4. Ensures Safety and Compliance
Whether it’s about maintaining building systems or else, there are some essentials that must not be overlooked at all, which are;
- Regular upkeep of fire safety systems and
- Adherence to safety standards protects employees and
- Ensure compliance with safety regulations.
After unveiling all the major benefits of facility maintenance, let’s discuss the very types of this maintenance!
3 Types of Facility Maintenance
For all the field teams out there who are busy ensuring proper field service reporting, we want to share very crucial details about maintaining the facility and its types!
1. Preventive Maintenance
Preventive maintenance involves regular inspections and servicing to prevent equipment failures. By following maintenance schedules, facility managers ensure that building systems, HVAC systems, and electrical systems stay operational, reducing the risk of costly emergency repairs.
2. Corrective Maintenance
This type of maintenance addresses issues after they occur but before they escalate into bigger problems. For example, maintenance technicians might repair a faulty HVAC unit before it causes a complete breakdown. Corrective maintenance helps minimize downtime and control maintenance costs.
3. Predictive Maintenance
Predictive maintenance uses data and analytics from facility management software and computerized maintenance management systems (CMMS) to predict when equipment might fail. This allows maintenance teams to fix problems before they impact equipment performance, ensuring smooth operations.
Never let your teams face breakdowns due to equipment failure!
Optimize your workflow with the best asset management software now!
How Facility Maintenance Software Can Help Companies?
Facility maintenance software simplifies maintenance operations by automating maintenance schedules, tracking asset performance, and managing maintenance tasks. It allows facility managers and maintenance technicians to oversee multiple building systems, such as HVAC systems, plumbing systems, and electrical systems, from a single platform.
Such kind of field service mobile apps also support preventive maintenance, helping businesses prevent equipment failures and reduce equipment downtime. By integrating computerized maintenance management systems, businesses can streamline maintenance management, ensuring timely routine maintenance and efficient resource allocation.
Moreover, facility maintenance software enhances asset management by monitoring capital assets and identifying potential risks, which leads to fewer emergency repairs and lower maintenance costs. For businesses aiming for operational efficiency, this software plays a critical role in keeping facility maintenance programs on track.
Parting Thoughts,
A solid facility maintenance program is in high demand because it indeed is essential for any business that is aiming for smooth operations & long-term cost savings. And this kind of efficiency can only be ensured when companies have access to modern facility management software field force management software, or both!
This kind of modern approach will not only prevent major equipment failures but will also help companies to experience better efficiency. Because after having such software, the teams will gain the capability of extending the lifespan of capital assets by ensuring that facility maintenance workers & maintenance technicians are operating at peak performance.
And for that reason, we are quoting that for both HR managers & CEOs, investing in the right facility maintenance software is the needed right step which they have to take now. So, they can easily adopt the best maintenance strategies to make a significant difference in meeting business goals & maintaining operational efficiency.
FAQs
How can facility maintenance software help reduce maintenance costs?
What challenges do facility managers face in facility maintenance?
Facility managers often have to deal with budget constraints, outdated equipment & some unavoidable scheduling issues. However, these maintenance professionals face multiple challenges in;
- Managing maintenance teams,
- Ensuring compliance with safety regulations, and
- Preventing unexpected equipment downtime.
How do facility managers contribute to operational efficiency?
Facility managers continue to ensure building systems like HVAC systems, electrical systems & plumbing systems so they can be inspected & maintained regularly.
What’s the difference between reactive and preventive maintenance?
Reactive maintenance continues to address problems after they occur, and that often keeps leading to emergency repairs & downtime. On the other hand preventive maintenance, involves regular checks & servicing to prevent equipment failures & reducing unexpected disruptions.
What role does preventive maintenance play in business success?
Preventive maintenance plays a crucial role in helping businesses to avoid costly major equipment failures. Because it ensures compliance with safety regulations & also helps in reducing maintenance costs. Furthermore, it also supports operational procedures by keeping facility assets in optimal working condition.