Grab a chance to avail 6 Months of Performance Module for FREE
Book a free demo session & learn more about it!
-
Will customized solution for your needs.
-
Empowering users with user-friendly features.
-
Driving success across diverse industries, everywhere.
Grab a chance to avail 6 Months of Performance Module for FREE
Book a free demo session & learn more about it!
Superworks
Modern HR Workplace
Your Partner in the entire Employee Life Cycle
From recruitment to retirement manage every stage of employee lifecycle with ease.
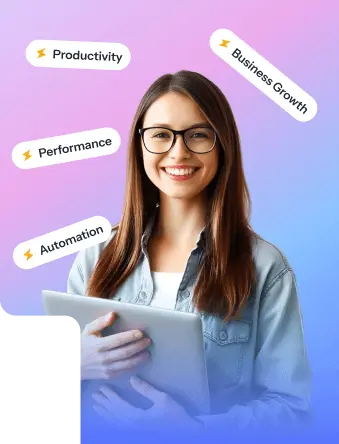
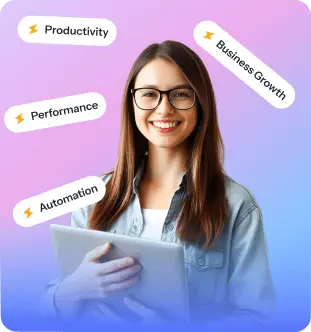
Seamless onboarding & offboarding
Automated compliance & payroll
Track performance & engagement
Manufacturing Management KRA/KPI
- Key Responsibility Areas (KRA) & Key Performance Indicators (KPI) for Manufacturing Manager
- 1. Production Planning and Control
- 2. Quality Management
- 3. Cost Control and Optimization
- 4. Team Management and Development
- 5. Equipment Maintenance and Reliability
- 6. Health and Safety Compliance
- 7. Process Improvement Initiatives
- 8. Supply Chain Management
- 9. Environmental Sustainability
- 10. Stakeholder Relationship Management
- Real-Time Example of KRA & KPI
- [Insert a real-world example related to the Manufacturing Manager]
- Key Takeaways
Key Responsibility Areas (KRA) & Key Performance Indicators (KPI) for Manufacturing Manager
1. Production Planning and Control
KRA: Ensuring efficient production planning and control to meet production targets and deadlines.
Short Description: Optimizing production schedules for maximum output.
- Number of Production Targets Met
- Production Efficiency Percentage
- On-time Delivery Rate
- Inventory Turnover Ratio
2. Quality Management
KRA: Maintaining and improving product quality standards in the manufacturing process.
Short Description: Ensuring consistent high-quality output.
- Defect Rate
- Customer Satisfaction Score
- First Pass Yield (FPY)
- Corrective Action Preventive Action (CAPA) Implementation
3. Cost Control and Optimization
KRA: Managing costs effectively to optimize production expenses.
Short Description: Improving cost-efficiency in manufacturing processes.
- Cost of Goods Sold (COGS)
- Waste Reduction Percentage
- Energy Consumption per Unit
- Cost Variance Analysis
4. Team Management and Development
KRA: Leading and developing the manufacturing team to enhance productivity and skills.
Short Description: Building a high-performing manufacturing team.
- Employee Turnover Rate
- Training Hours per Employee
- Team Productivity Index
- Employee Engagement Score
5. Equipment Maintenance and Reliability
KRA: Ensuring proper maintenance and reliability of manufacturing equipment.
Short Description: Maximizing equipment uptime and longevity.
- Downtime Percentage
- Mean Time Between Failures (MTBF)
- Maintenance Cost per Equipment
- Equipment Utilization Rate
6. Health and Safety Compliance
KRA: Upholding health and safety standards in the manufacturing environment.
Short Description: Ensuring a safe workplace for all employees.
- Number of Safety Incidents
- Lost Time Injury Frequency Rate
- Safety Training Compliance Rate
- Emergency Response Time
7. Process Improvement Initiatives
KRA: Identifying and implementing process improvements to enhance operational efficiency.
Short Description: Driving continuous improvement in manufacturing processes.
- Number of Process Improvements Implemented
- Cost Savings from Process Improvements
- Process Efficiency Gain Percentage
- Lean Manufacturing Principles Adoption Rate
8. Supply Chain Management
KRA: Managing and optimizing the manufacturing supply chain for seamless operations.
Short Description: Ensuring timely and efficient flow of materials.
- Supplier Delivery Performance
- Inventory Turnover Rate
- Lead Time Reduction
- Supply Chain Cost Reduction
9. Environmental Sustainability
KRA: Implementing environmentally sustainable practices in manufacturing operations.
Short Description: Promoting eco-friendly manufacturing processes.
- Carbon Footprint Reduction
- Water and Energy Consumption Efficiency
- Waste Recycling Percentage
- Environmental Compliance Audit Score
10. Stakeholder Relationship Management
KRA: Building and maintaining positive relationships with key stakeholders.
Short Description: Ensuring alignment and collaboration with stakeholders.
- Stakeholder Satisfaction Index
- Partnership Renewal Rate
- Community Engagement Activities
- Stakeholder Feedback Implementation Rate
Real-Time Example of KRA & KPI
KRA: Provide an example of how an organization or professional applies this KRA in real life.
- KPI 1: [Example of a measurable KPI]
- KPI 2: [Example of a measurable KPI]
- KPI 3: [Example of a measurable KPI]
- KPI 4: [Example of a measurable KPI]
Describe how these KPIs led to improved performance and success.
Key Takeaways
- KRA defines what needs to be done, whereas KPI measures how well it is done.
- KPIs should always be SMART (Specific, Measurable, Achievable, Relevant, Time-bound).
- Regular tracking and adjustments ensure success in Manufacturing Manager.
Content generated in a structured format with clear, concise, and measurable KPIs while maintaining professional readability.