Grab a chance to avail 6 Months of Performance Module for FREE
Book a free demo session & learn more about it!
-
Will customized solution for your needs.
-
Empowering users with user-friendly features.
-
Driving success across diverse industries, everywhere.
Grab a chance to avail 6 Months of Performance Module for FREE
Book a free demo session & learn more about it!
Superworks
Modern HR Workplace
Your Partner in the entire Employee Life Cycle
From recruitment to retirement manage every stage of employee lifecycle with ease.
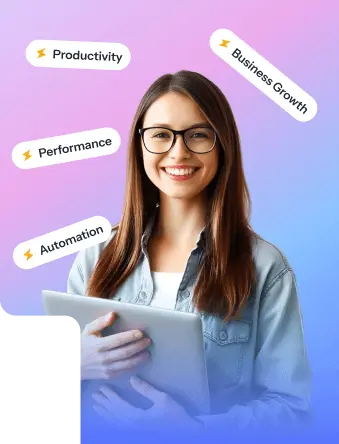
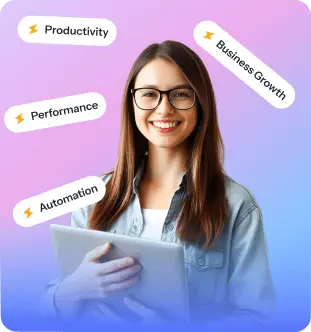
Seamless onboarding & offboarding
Automated compliance & payroll
Track performance & engagement
Millwright KRA/KPI
- Key Responsibility Areas (KRA) & Key Performance Indicators (KPI)
- 1. Maintenance and Repair
- 2. Safety Compliance
- 3. Equipment Installation
- 4. Troubleshooting and Diagnostics
- 5. Spare Parts Management
- 6. Training and Development
- 7. Performance Monitoring
- 8. Continuous Improvement
- 9. Team Collaboration
- 10. Reporting and Documentation
- Real-Time Example of KRA & KPI
- Example: Maintenance and Repair
- Key Takeaways
Key Responsibility Areas (KRA) & Key Performance Indicators (KPI)
1. Maintenance and Repair
KRA: Ensuring the maintenance and repair of machinery and equipment to minimize downtime and optimize operational efficiency.
Short Description: Machinery maintenance and repair.
- 1. Percentage of scheduled maintenance completed on time.
- 2. Average time taken to repair equipment breakdowns.
- 3. Reduction in overall maintenance costs.
- 4. Number of equipment failures per month.
2. Safety Compliance
KRA: Upholding safety standards and regulations to create a secure work environment for all personnel.
Short Description: Ensuring safety compliance.
- 1. Number of safety incidents reported.
- 2. Completion rate of safety training programs.
- 3. Compliance with safety audits and inspections.
- 4. Implementation of safety improvement initiatives.
3. Equipment Installation
KRA: Installing new machinery and equipment according to specifications to support production requirements.
Short Description: Proper installation of equipment.
- 1. Percentage of successful equipment installations.
- 2. Adherence to installation timelines.
- 3. Accuracy of equipment calibration post-installation.
- 4. Feedback on equipment performance from production teams.
4. Troubleshooting and Diagnostics
KRA: Identifying and resolving technical issues in machinery through effective troubleshooting and diagnostics.
Short Description: Problem-solving in machinery.
- 1. Average time to diagnose equipment malfunctions.
- 2. Accuracy of root cause analysis for breakdowns.
- 3. Successful resolution of equipment issues.
- 4. Number of repeat incidents after troubleshooting.
5. Spare Parts Management
KRA: Managing inventory and procurement of spare parts to ensure availability for maintenance and repairs.
Short Description: Efficient spare parts management.
- 1. Inventory turnover rate for spare parts.
- 2. Percentage of critical spare parts in stock.
- 3. Cost savings through optimized spare parts procurement.
- 4. Accuracy of spare parts ordering process.
6. Training and Development
KRA: Providing training and development opportunities to enhance technical skills and knowledge in the millwright field.
Short Description: Continuous skill enhancement.
- 1. Participation rate in training programs.
- 2. Skill improvement based on assessments.
- 3. Application of new skills in daily tasks.
- 4. Feedback on the effectiveness of training initiatives.
7. Performance Monitoring
KRA: Monitoring equipment performance and efficiency metrics to proactively address potential issues and optimize productivity.
Short Description: Monitoring equipment performance.
- 1. Overall equipment effectiveness (OEE) scores.
- 2. Downtime reduction percentage due to proactive measures.
- 3. Feedback from production teams on equipment reliability.
- 4. Adherence to performance monitoring schedules.
8. Continuous Improvement
KRA: Identifying areas for improvement in maintenance processes and implementing measures to enhance operational efficiency.
Short Description: Process improvement initiatives.
- 1. Number of implemented process improvements.
- 2. Percentage increase in maintenance efficiency post-improvements.
- 3. Feedback on the impact of improvements from stakeholders.
- 4. Cost savings achieved through efficiency enhancements.
9. Team Collaboration
KRA: Collaborating with cross-functional teams to ensure coordinated efforts in equipment maintenance and project execution.
Short Description: Team coordination in maintenance projects.
- 1. Feedback on teamwork effectiveness from team members.
- 2. Completion rate of interdepartmental projects.
- 3. Resolution time for collaborative maintenance tasks.
- 4. Adherence to project timelines through teamwork.
10. Reporting and Documentation
KRA: Maintaining accurate records and documentation of maintenance activities and equipment performance for reference and analysis.
Short Description: Documentation of maintenance activities.
- 1. Completion rate of maintenance reports on time.
- 2. Accuracy of maintenance logs and records.
- 3. Utilization of maintenance data for predictive analysis.
- 4. Feedback on the effectiveness of documentation practices.
Real-Time Example of KRA & KPI
Example: Maintenance and Repair
KRA: Ensuring scheduled maintenance tasks are completed on time to minimize equipment downtime and maintain operational efficiency.
- KPI 1: Percentage of scheduled maintenance completed on time (Target: 95%).
- KPI 2: Average time taken to repair equipment breakdowns (Target: <4 hours).
- KPI 3: Reduction in overall maintenance costs (Target: 10% reduction).
- KPI 4: Number of equipment failures per month (Target: <2 failures).
Tracking these KPIs led to improved equipment reliability, reduced downtime, and cost savings for the organization.
Key Takeaways
- KRA defines what needs to be done, whereas KPI measures how well it is done.
- KPIs should always be SMART (Specific, Measurable, Achievable, Relevant, Time-bound).
- Regular tracking and adjustments ensure success in Millwright.
Generate content in this structured format with clear, concise, and measurable KPIs while maintaining professional readability.