Grab a chance to avail 6 Months of Performance Module for FREE
Book a free demo session & learn more about it!
-
Will customized solution for your needs.
-
Empowering users with user-friendly features.
-
Driving success across diverse industries, everywhere.
Grab a chance to avail 6 Months of Performance Module for FREE
Book a free demo session & learn more about it!
Superworks
Modern HR Workplace
Your Partner in the entire Employee Life Cycle
From recruitment to retirement manage every stage of employee lifecycle with ease.
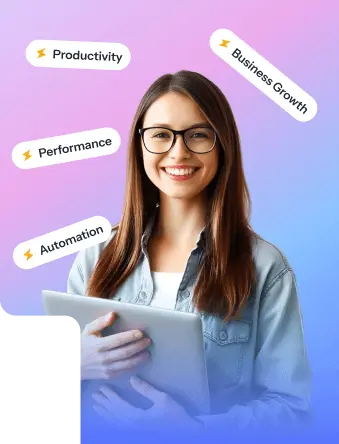
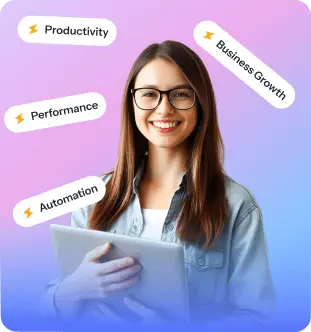
Seamless onboarding & offboarding
Automated compliance & payroll
Track performance & engagement
Packaging Assistant KRA/KPI
- Key Responsibility Areas (KRAs) & Key Performance Indicators (KPIs) for Packaging Assistant
- 1. Inventory Management
- 2. Quality Control
- 3. Cost Efficiency
- 4. Productivity Enhancement
- 5. Safety and Compliance
- 6. Environmental Sustainability
- 7. Team Collaboration
- 8. Continuous Improvement
- 9. Customer Experience
- 10. Technology Integration
Key Responsibility Areas (KRAs) & Key Performance Indicators (KPIs) for Packaging Assistant
1. Inventory Management
KRA: Ensuring accurate tracking and maintenance of packaging materials inventory to support operational efficiency.
Short Description: Manage and optimize packaging material stock levels.
- Number of stockouts per month
- Inventory turnover ratio
- Percentage of obsolete inventory
- Accuracy of inventory records
2. Quality Control
KRA: Maintaining quality standards in packaging processes to deliver consistent and high-quality products.
Short Description: Ensure packaging meets quality requirements.
- Defect rate in packaging
- Customer satisfaction score related to packaging
- Compliance with packaging regulations
- Number of packaging-related complaints
3. Cost Efficiency
KRA: Implementing cost-effective packaging solutions to optimize expenses without compromising quality.
Short Description: Reduce packaging costs while maintaining quality.
- Cost per unit of packaging
- Percentage reduction in packaging expenses
- Return on investment for packaging improvements
- Percentage of budget variance for packaging
4. Productivity Enhancement
KRA: Improving packaging processes to enhance productivity and meet production targets efficiently.
Short Description: Optimize packaging workflows for increased efficiency.
- Packaging output per hour
- Time taken for packaging per unit
- Percentage increase in packaging speed
- Number of packaging process optimizations implemented
5. Safety and Compliance
KRA: Ensuring packaging operations adhere to safety standards and regulatory requirements.
Short Description: Maintain a safe packaging environment.
- Number of safety incidents in packaging
- Compliance score with packaging regulations
- Employee training hours on packaging safety
- Audit results related to packaging compliance
6. Environmental Sustainability
KRA: Implementing eco-friendly packaging solutions to reduce environmental impact.
Short Description: Promote sustainable packaging practices.
- Percentage of recyclable packaging materials used
- Carbon footprint reduction from packaging activities
- Number of sustainable packaging initiatives implemented
- Customer perception of eco-friendly packaging
7. Team Collaboration
KRA: Collaborating effectively with cross-functional teams to ensure seamless packaging operations.
Short Description: Foster teamwork and communication for packaging success.
- Team satisfaction with packaging support
- Number of successful packaging projects with cross-functional teams
- Communication effectiveness in packaging meetings
- Feedback from other departments on packaging collaboration
8. Continuous Improvement
KRA: Identifying opportunities for continuous improvement in packaging processes and implementing enhancements.
Short Description: Drive ongoing improvements in packaging operations.
- Number of packaging process enhancements implemented
- Percentage increase in packaging efficiency over time
- Employee suggestions implemented in packaging improvements
- Reduction in packaging errors over consecutive quarters
9. Customer Experience
KRA: Contributing to a positive customer experience through well-packaged products that meet customer expectations.
Short Description: Enhance customer satisfaction through packaging.
- Customer feedback on packaging experience
- Number of product returns due to packaging issues
- Packaging impact on customer reviews and ratings
- Customer retention rate related to packaging quality
10. Technology Integration
KRA: Leveraging technology for automation and innovation in packaging processes to stay competitive.
Short Description: Implement technology solutions for packaging advancements.
- Percentage of automated packaging tasks
- Adoption rate of new packaging technologies
- Reduction in packaging errors due to technology implementation
- Cost savings from technology-driven packaging improvements