Grab a chance to avail 6 Months of Performance Module for FREE
Book a free demo session & learn more about it!
-
Will customized solution for your needs
-
Empowering users with user-friendly features
-
Driving success across diverse industries, everywhere.
Grab a chance to avail 6 Months of Performance Module for FREE
Book a free demo session & learn more about it!
Superworks
Modern HR Workplace
Your Partner in the entire Employee Life Cycle
From recruitment to retirement manage every stage of employee lifecycle with ease.
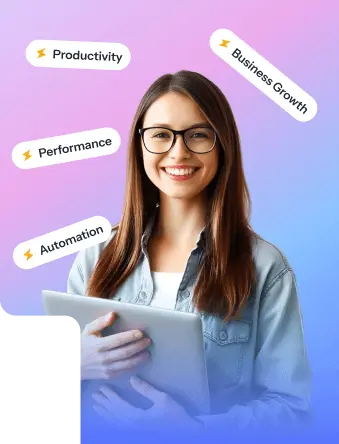
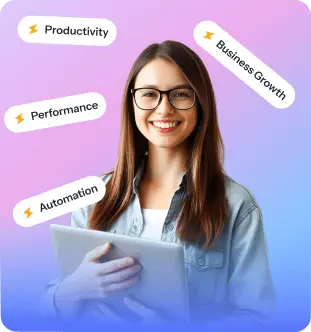
Seamless onboarding & offboarding
Automated compliance & payroll
Track performance & engagement
Of Production Operator KRA/KPI
Key Responsibility Areas (KRA) & Key Performance Indicators (KPI)
1. Production Equipment Operation
KRA: Efficiently operate production equipment to meet daily production targets.
Short Description: Ensuring smooth operation of machinery for production processes.
- Machine Downtime Percentage
- Production Output per Hour
- Quality Assurance Compliance Rate
- Equipment Maintenance Schedule Adherence
2. Safety Compliance
KRA: Adhere to safety protocols and guidelines to maintain a safe working environment.
Short Description: Ensuring a secure workplace through safety procedures.
- Number of Safety Incidents
- Safety Training Completion Rate
- Emergency Response Time
- PPE Usage Compliance
3. Quality Control
KRA: Ensure the quality of products through rigorous quality control checks.
Short Description: Maintaining product quality standards.
- Defect Rate
- Customer Complaint Resolution Time
- Quality Audit Score
- First Pass Yield Rate
4. Production Efficiency
KRA: Improve production efficiency by optimizing processes and minimizing waste.
Short Description: Enhancing productivity while reducing resource wastage.
- Production Yield Percentage
- Production Cycle Time Reduction
- Energy Consumption Efficiency
- Raw Material Waste Reduction
5. Team Collaboration
KRA: Collaborate with team members to ensure smooth production flow and effective communication.
Short Description: Promoting teamwork and communication within the production team.
- Team Efficiency Rating
- Communication Effectiveness Score
- Teamwork Assessment Results
- Conflict Resolution Time
Real-Time Example of KRA & KPI
Real-World Example: Production Operator at XYZ Manufacturing
KRA: In a manufacturing plant, Production Operators are evaluated based on their ability to meet daily production targets while maintaining quality standards.
- KPI 1: Machine Downtime Percentage – Achieving less than 5% downtime by performing regular maintenance.
- KPI 2: Defect Rate – Maintaining a defect rate below 2% through quality control checks.
- KPI 3: Production Output per Hour – Achieving 100 units per hour to meet production goals.
- KPI 4: Team Efficiency Rating – Ensuring team collaboration results in a rating of 4 out of 5.
By meeting these KPIs, the Production Operator at XYZ Manufacturing has contributed to increased productivity and efficiency in the production process.
Key Takeaways
- KRA defines what needs to be done, whereas KPI measures how well it is done.
- KPIs should always be SMART (Specific, Measurable, Achievable, Relevant, Time-bound).
- Regular tracking and adjustments ensure success in the role of a Production Operator.
Ensure that the content is structured, informative, and includes measurable KPIs for a clear understanding of performance expectations in the role of a Production Operator.