Grab a chance to avail 6 Months of Performance Module for FREE
Book a free demo session & learn more about it!
-
Will customized solution for your needs.
-
Empowering users with user-friendly features.
-
Driving success across diverse industries, everywhere.
Grab a chance to avail 6 Months of Performance Module for FREE
Book a free demo session & learn more about it!
Superworks
Modern HR Workplace
Your Partner in the entire Employee Life Cycle
From recruitment to retirement manage every stage of employee lifecycle with ease.
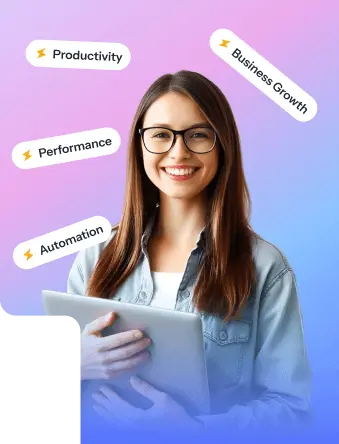
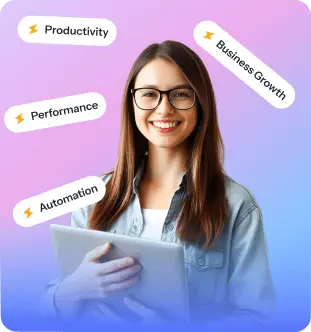
Seamless onboarding & offboarding
Automated compliance & payroll
Track performance & engagement
Production Staff KRA/KPI
- Job Description: Production Staff
- Key Responsibility Areas (KRA) & Key Performance Indicators (KPI)
- 1. Production Planning and Scheduling
- 2. Quality Control and Assurance
- 3. Equipment Maintenance and Optimization
- 4. Team Management and Development
- 5. Cost Control and Budget Management
- Real-Time Example of KRA & KPI
- Example: Production Staff Improving Efficiency
- Key Takeaways
Job Description: Production Staff
This job involves overseeing production processes, ensuring efficiency, quality, and safety standards are met in a manufacturing setting. The role requires strong organizational skills, attention to detail, and the ability to work well under pressure to meet production targets.
Key Responsibility Areas (KRA) & Key Performance Indicators (KPI)
1. Production Planning and Scheduling
KRA: Responsible for creating production schedules and plans to meet demand efficiently.
Short Description: Efficiently plan and schedule production activities.
- Production Efficiency Rate
- On-time Delivery Performance
- Production Cost Variance
- Inventory Turnover Ratio
2. Quality Control and Assurance
KRA: Ensure products meet quality standards and lead quality improvement initiatives.
Short Description: Maintain high product quality standards.
- Defect Rate
- Customer Satisfaction Score
- First Pass Yield
- Compliance with Standards
3. Equipment Maintenance and Optimization
KRA: Manage equipment maintenance schedules to prevent downtime.
Short Description: Optimize equipment performance and uptime.
- Downtime Percentage
- Equipment Utilization Rate
- Maintenance Cost per Unit Produced
- Mean Time Between Failures (MTBF)
4. Team Management and Development
KRA: Lead and motivate production staff to achieve their best performance.
Short Description: Develop and manage production team effectively.
- Employee Satisfaction Score
- Training Hours per Employee
- Team Productivity Rate
- Employee Turnover Rate
5. Cost Control and Budget Management
KRA: Monitor production costs and implement cost-saving measures.
Short Description: Control production costs within budget.
- Cost per Unit Produced
- Variance from Budget
- Cost Reduction Initiatives Implemented
- Material Waste Percentage
Real-Time Example of KRA & KPI
Example: Production Staff Improving Efficiency
KRA: By optimizing production schedules and reducing downtime, a production staff team increased production efficiency by 15%.
- KPI 1: Downtime Percentage reduced from 10% to 5%
- KPI 2: Production Efficiency Rate increased from 80% to 92%
- KPI 3: Training Hours per Employee doubled, leading to improved performance
- KPI 4: Cost per Unit Produced decreased by 8% due to better planning
This improvement in KPIs led to higher productivity levels, cost savings, and better employee morale.
Key Takeaways
- KRA defines what needs to be done, whereas KPI measures how well it is done.
- KPIs should always be SMART (Specific, Measurable, Achievable, Relevant, Time-bound).
- Regular tracking and adjustments ensure success in Production Staff.
Content structured for easy understanding and actionable performance improvement in a production setting.