Grab a chance to avail 6 Months of Performance Module for FREE
Book a free demo session & learn more about it!
-
Will customized solution for your needs.
-
Empowering users with user-friendly features.
-
Driving success across diverse industries, everywhere.
Grab a chance to avail 6 Months of Performance Module for FREE
Book a free demo session & learn more about it!
Superworks
Modern HR Workplace
Your Partner in the entire Employee Life Cycle
From recruitment to retirement manage every stage of employee lifecycle with ease.
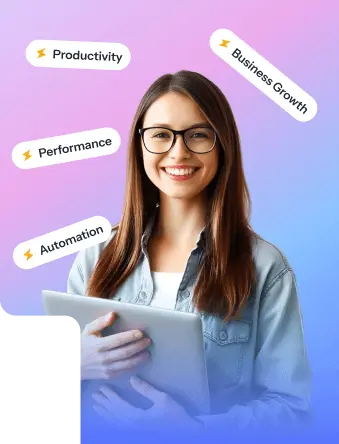
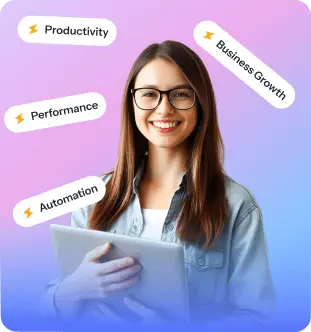
Seamless onboarding & offboarding
Automated compliance & payroll
Track performance & engagement
Quality Control Civil Engineer KRA/KPI
- Key Responsibility Areas (KRAs) & Key Performance Indicators (KPIs) for Quality Control Civil Engineer
- 1. Quality Assurance Management
- 2. Inspection and Testing Procedures
- 3. Documentation and Reporting
- 4. Process Improvement Initiatives
- 5. Compliance with Regulatory Standards
- 6. Team Training and Development
- 7. Supplier Quality Management
- 8. Root Cause Analysis
- 9. Budget and Resource Management
- 10. Stakeholder Communication
- Real-Time Example of KRA & KPI
- Example: Quality Assurance Management
- Key Takeaways
Key Responsibility Areas (KRAs) & Key Performance Indicators (KPIs) for Quality Control Civil Engineer
1. Quality Assurance Management
KRA: Ensuring compliance with quality standards in all civil engineering projects.
Short Description: Overseeing quality control processes for project success.
- Defect Density Rate
- Customer Satisfaction Score
- Percentage of Compliance with Standards
- Number of Non-Conformities Identified
2. Inspection and Testing Procedures
KRA: Implementing effective inspection and testing protocols for construction materials and structures.
Short Description: Ensuring structural integrity through rigorous testing.
- Accuracy of Testing Results
- Adherence to Inspection Schedules
- Reduction in Rejected Materials
- Timely Reporting of Test Results
3. Documentation and Reporting
KRA: Maintaining accurate records of quality control activities and preparing detailed reports.
Short Description: Ensuring transparency through documentation.
- Completion of Inspection Reports
- Accuracy of Documentation
- Timely Submission of Reports
- Feedback from Project Managers on Report Clarity
4. Process Improvement Initiatives
KRA: Identifying areas for process enhancement to optimize quality control procedures.
Short Description: Driving continuous improvement for efficiency.
- Implementation of Process Enhancements
- Reduction in Defect Rates Over Time
- Feedback from Team Members on Process Improvements
- Adoption Rate of New Quality Control Measures
5. Compliance with Regulatory Standards
KRA: Ensuring adherence to all industry regulations and safety guidelines.
Short Description: Upholding legal and safety requirements.
- Number of Regulatory Violations
- Completion of Safety Training
- Audit Compliance Score
- Incident Report Rate
6. Team Training and Development
KRA: Providing training programs to enhance the skills of the quality control team.
Short Description: Fostering a culture of continuous learning.
- Training Attendance Rate
- Improvement in Team Performance After Training
- Employee Feedback on Training Effectiveness
- Certification Achievement Rate
7. Supplier Quality Management
KRA: Evaluating and monitoring the quality of materials supplied by vendors and contractors.
Short Description: Ensuring quality inputs for successful outputs.
- Supplier Defect Rate
- Timely Delivery of Quality Materials
- Feedback from Project Teams on Material Quality
- Percentage of Approved Suppliers
8. Root Cause Analysis
KRA: Conducting root cause analysis to address quality issues and prevent recurrence.
Short Description: Identifying and resolving underlying problems.
- Time to Identify Root Cause
- Effectiveness of Corrective Actions
- Reduction in Recurring Quality Issues
- Feedback from Stakeholders on Problem Resolution
9. Budget and Resource Management
KRA: Efficiently managing resources and budgets allocated for quality control activities.
Short Description: Optimizing resource utilization for cost-effectiveness.
- Adherence to Quality Control Budget
- Resource Utilization Efficiency
- Cost Savings through Process Improvements
- Return on Investment in Quality Control Measures
10. Stakeholder Communication
KRA: Maintaining clear and open communication channels with project stakeholders regarding quality control.
Short Description: Building trust through effective communication.
- Stakeholder Satisfaction Survey Results
- Timely Resolution of Stakeholder Concerns
- Feedback from Stakeholders on Communication Effectiveness
- Number of Quality Control-related Meetings with Stakeholders
Real-Time Example of KRA & KPI
Example: Quality Assurance Management
KRA: Ensuring compliance with quality standards by conducting regular audits and inspections to identify and rectify deviations.
- KPI 1: Defect Density Rate reduced by 15% after implementing new quality control measures.
- KPI 2: Customer Satisfaction Score increased to 90% due to improved quality assurance practices.
- KPI 3: 100% Compliance with Industry Standards achieved in the latest project audit.
- KPI 4: Identified and addressed 20 Non-Conformities within the specified timeline.
These KPIs led to enhanced project quality, increased client satisfaction, and improved overall performance.
Key Takeaways
- KRA defines what needs to be done, whereas KPI measures how well it is done.
- KPIs should always be SMART (Specific, Measurable, Achievable, Relevant, Time-bound).
- Regular tracking and adjustments ensure success in Quality Control Civil Engineer.