Grab a chance to avail 6 Months of Performance Module for FREE
Book a free demo session & learn more about it!
-
Will customized solution for your needs.
-
Empowering users with user-friendly features.
-
Driving success across diverse industries, everywhere.
Grab a chance to avail 6 Months of Performance Module for FREE
Book a free demo session & learn more about it!
Superworks
Modern HR Workplace
Your Partner in the entire Employee Life Cycle
From recruitment to retirement manage every stage of employee lifecycle with ease.
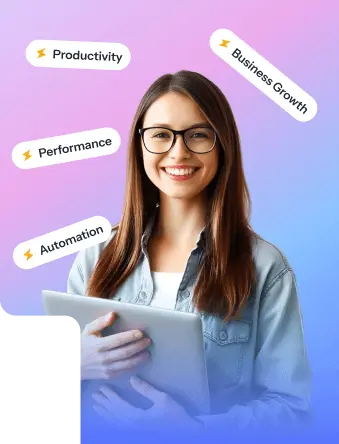
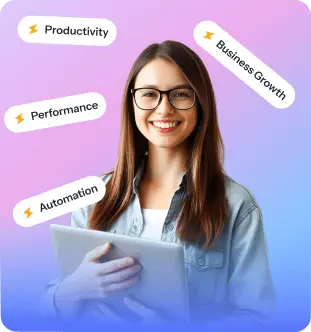
Seamless onboarding & offboarding
Automated compliance & payroll
Track performance & engagement
Quality Control Engineer KRA/KPI
Key Responsibility Areas (KRA) & Key Performance Indicators (KPI)
1. Quality Assurance Process
KRA: Implement and monitor quality assurance processes to ensure compliance with industry standards.
Short Description: Oversee quality assurance procedures for product manufacturing.
- Defect Rate: Maintain defect rate below X%.
- Compliance Audits: Achieve X% compliance in audits.
- Quality Improvement Initiatives: Implement X new quality improvement initiatives quarterly.
- Customer Satisfaction: Maintain customer satisfaction rating above X%.
2. Inspection and Testing
KRA: Conduct inspections and tests on products to identify defects and ensure adherence to quality standards.
Short Description: Perform product inspections and testing for quality control.
- Inspection Accuracy: Achieve X% accuracy in product inspections.
- Testing Efficiency: Complete testing within specified timeframes X% of the time.
- Defect Identification: Identify and report defects within X hours of discovery.
- Test Result Analysis: Analyze test results and provide recommendations for improvement X times per month.
3. Root Cause Analysis
KRA: Investigate and determine root causes of quality issues to implement corrective actions.
Short Description: Identify and address root causes of quality problems.
- Root Cause Identification: Identify root causes of quality issues within X days.
- Corrective Action Implementation: Implement corrective actions for identified root causes within X hours.
- Preventive Measures: Propose X preventive measures to avoid recurring quality issues.
- Quality Incident Resolution: Resolve quality incidents within X days of occurrence.
4. Process Improvement
KRA: Continuously improve quality control processes to enhance efficiency and effectiveness.
Short Description: Drive process improvements for quality control.
- Process Efficiency: Improve process efficiency by X% within a specified timeframe.
- Cost Savings: Identify cost-saving opportunities through process improvements X times per quarter.
- Training Effectiveness: Evaluate training effectiveness in quality control X times per year.
- Process Documentation: Update process documentation for quality control procedures quarterly.
5. Supplier Quality Management
KRA: Monitor and evaluate supplier quality to ensure adherence to quality standards.
Short Description: Manage supplier quality for incoming materials.
- Supplier Evaluation: Evaluate supplier quality performance biannually.
- Quality Metrics: Define and track supplier quality metrics monthly.
- Non-Conformance Resolution: Resolve supplier non-conformance issues within X days.
- Supplier Audits: Conduct supplier audits according to schedule X times per year.
Real-Time Example of KRA & KPI
Real-World Example: Improving Production Efficiency
KRA: Implement lean manufacturing principles to reduce production waste and improve efficiency.
- KPI 1: Reduce production waste by X% within six months.
- KPI 2: Increase production efficiency by X% through process optimization.
- KPI 3: Achieve X% improvement in product quality as a result of lean practices.
- KPI 4: Decrease production lead time by X days through lean implementation.
By tracking these KPIs, the organization was able to streamline production processes, reduce costs, and enhance overall product quality, leading to increased customer satisfaction and higher profitability.
Key Takeaways
- KRA defines what needs to be done, whereas KPI measures how well it is done.
- KPIs should always be SMART (Specific, Measurable, Achievable, Relevant, Time-bound).
- Regular tracking and adjustments ensure success in Quality Control Engineer.
Implementing these KRA and KPI frameworks will help you excel in your role as a Quality Control Engineer and drive continuous improvement in quality standards and processes.