Grab a chance to avail 6 Months of Performance Module for FREE
Book a free demo session & learn more about it!
-
Will customized solution for your needs.
-
Empowering users with user-friendly features.
-
Driving success across diverse industries, everywhere.
Grab a chance to avail 6 Months of Performance Module for FREE
Book a free demo session & learn more about it!
Superworks
Modern HR Workplace
Your Partner in the entire Employee Life Cycle
From recruitment to retirement manage every stage of employee lifecycle with ease.
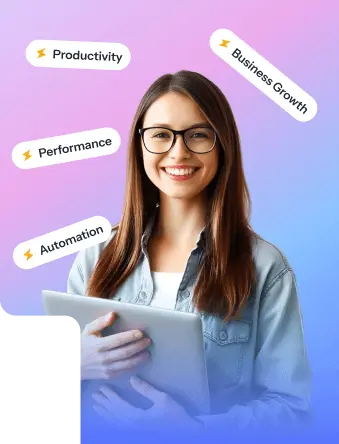
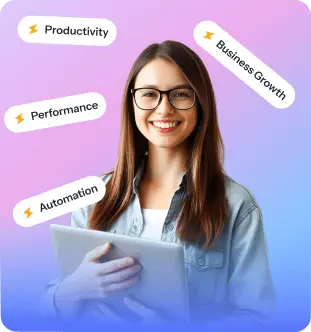
Seamless onboarding & offboarding
Automated compliance & payroll
Track performance & engagement
Quality Engineer Manufacturing KRA/KPI
- Key Responsibility Areas (KRA) & Key Performance Indicators (KPI) for Quality Engineer (Manufacturing)
- 1. Quality Management Systems
- 2. Product Quality Assurance
- 3. Supplier Quality Management
- 4. Process Improvement
- 5. Data Analysis and Reporting
- Real-Time Example of KRA & KPI
- Implementing Continuous Improvement Initiatives
- Key Takeaways
Key Responsibility Areas (KRA) & Key Performance Indicators (KPI) for Quality Engineer (Manufacturing)
1. Quality Management Systems
KRA: Implement and maintain quality management systems to ensure compliance with industry standards and regulations.
Short Description: Establish and oversee quality management processes.
- Defect rate reduction by X%.
- Audit compliance score above X%.
- Number of non-conformances resolved per month.
- Implementation of X new quality initiatives.
2. Product Quality Assurance
KRA: Monitor and improve product quality through testing, analysis, and corrective actions.
Short Description: Ensure product quality meets or exceeds standards.
- First-pass yield rate above X%.
- Customer complaints reduced by X%.
- Number of process improvements implemented per quarter.
- Defect rate in final product below X ppm.
3. Supplier Quality Management
KRA: Collaborate with suppliers to maintain quality standards in the supply chain.
Short Description: Ensure supplier quality aligns with organizational requirements.
- Supplier defect rate below X%.
- On-time delivery performance above X%.
- Number of supplier audits conducted per quarter.
- Implementation of X supplier improvement initiatives.
4. Process Improvement
KRA: Identify and implement process improvements to enhance efficiency and quality.
Short Description: Continuously improve manufacturing processes.
- Reduction in production cycle time by X%.
- Cost savings from process improvements exceeding X.
- Number of successful lean manufacturing projects completed.
- Increase in overall equipment effectiveness (OEE) by X%.
5. Data Analysis and Reporting
KRA: Analyze quality data to identify trends, patterns, and areas for improvement.
Short Description: Utilize data for informed decision-making.
- Accuracy of quality reports above X%.
- Number of actionable insights derived from data analysis.
- Reduction in data entry errors by X%.
- Timely submission of quality reports per schedule.
Real-Time Example of KRA & KPI
Implementing Continuous Improvement Initiatives
KRA: Implementing a continuous improvement program to enhance product quality and operational efficiency.
- KPI 1: Increase in product quality ratings by X points.
- KPI 2: Cost savings from process improvements exceeding X amount.
- KPI 3: Number of employee suggestions implemented for process enhancement.
- KPI 4: Reduction in defect rate by X% within 6 months.
This initiative led to a 15% increase in customer satisfaction, a 20% reduction in production costs, and a 25% improvement in overall process efficiency.
Key Takeaways
- KRA defines what needs to be done, whereas KPI measures how well it is done.
- KPIs should always be SMART (Specific, Measurable, Achievable, Relevant, Time-bound).
- Regular tracking and adjustments ensure success in Quality Engineer (manufacturing).
Ensure to measure the success of the Quality Engineer through these KPIs and adapt as necessary for continual improvement.