Grab a chance to avail 6 Months of Performance Module for FREE
Book a free demo session & learn more about it!
-
Will customized solution for your needs
-
Empowering users with user-friendly features
-
Driving success across diverse industries, everywhere.
Grab a chance to avail 6 Months of Performance Module for FREE
Book a free demo session & learn more about it!
Superworks
Modern HR Workplace
Your Partner in the entire Employee Life Cycle
From recruitment to retirement manage every stage of employee lifecycle with ease.
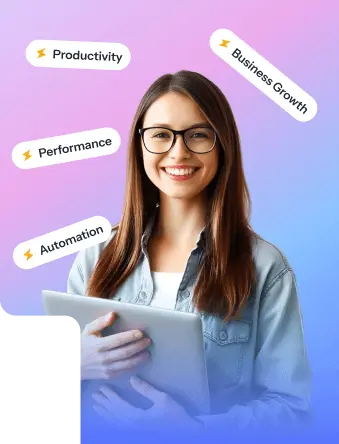
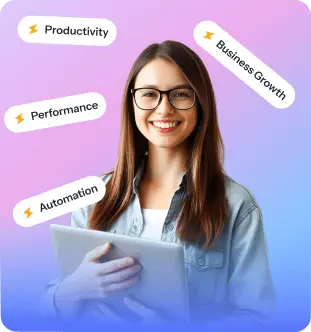
Seamless onboarding & offboarding
Automated compliance & payroll
Track performance & engagement
Quality Inspector KRA/KPI
- Job Description
- Key Responsibility Areas (KRA) & Key Performance Indicators (KPI)
- 1. Quality Inspection
- 2. Process Improvement
- 3. Documentation and Reporting
- 4. Supplier and Vendor Management
- 5. Regulatory Compliance
- 6. Team Training and Development
- 7. Continuous Monitoring
- 8. Customer Satisfaction
- 9. Cost Optimization
- 10. Innovation and Technology Integration
- Real-Time Example of KRA & KPI
- Real-World Quality Inspector Example
- Key Takeaways
Job Description
A Quality Inspector is responsible for ensuring that products meet quality standards and specifications. They conduct inspections, identify defects, and provide feedback to improve processes and product quality.
Key Responsibility Areas (KRA) & Key Performance Indicators (KPI)
1. Quality Inspection
KRA: Conduct thorough quality inspections to identify defects and deviations.
Short Description: Ensuring product quality through detailed inspections.
- Defect Rate: Percentage of defective products identified.
- Inspection Accuracy: Percentage of accurately identified defects.
- Inspection Time: Time taken to complete inspections per unit.
- Quality Compliance: Adherence to quality standards and specifications.
2. Process Improvement
KRA: Collaborate with teams to implement process improvements based on inspection findings.
Short Description: Driving continuous improvement in quality processes.
- Process Efficiency: Percentage improvement in production processes.
- Defect Reduction: Percentage decrease in defects over time.
- Feedback Implementation: Rate of implementation of feedback suggestions.
- Training Effectiveness: Improvement in staff training outcomes.
3. Documentation and Reporting
KRA: Maintain accurate records of inspections and generate comprehensive reports.
Short Description: Ensuring proper documentation and reporting.
- Report Accuracy: Precision in reporting inspection results.
- Documentation Timeliness: Meeting timelines for report submission.
- Data Integrity: Accuracy and completeness of inspection data.
- Report Clarity: Clear communication of findings and recommendations.
4. Supplier and Vendor Management
KRA: Evaluate and monitor supplier quality performance.
Short Description: Ensuring quality standards from suppliers and vendors.
- Supplier Compliance: Adherence to quality requirements by suppliers.
- Vendor Rating: Performance rating of vendors based on quality.
- Material Inspection: Effectiveness of material quality checks.
- Supplier Communication: Timely feedback and communication with suppliers.
5. Regulatory Compliance
KRA: Ensure compliance with industry regulations and standards.
Short Description: Maintaining regulatory quality standards.
- Regulatory Adherence: Compliance with industry regulations.
- Audit Preparedness: Readiness for quality audits and inspections.
- Standard Updates: Implementation of latest quality standards.
- Documentation Compliance: Accuracy of regulatory documentation.
6. Team Training and Development
KRA: Provide training and guidance to team members on quality control processes.
Short Description: Developing team competence in quality control.
- Training Effectiveness: Improvement in team members’ quality control skills.
- Knowledge Transfer: Successful transfer of quality expertise.
- Team Engagement: Level of team involvement in quality initiatives.
- Performance Improvement: Increase in team quality performance metrics.
7. Continuous Monitoring
KRA: Continuously monitor quality metrics and initiate corrective actions.
Short Description: Proactive monitoring and corrective actions for quality.
- Monitoring Frequency: Regularity of quality metric monitoring.
- Action Responsiveness: Timely response to quality issues.
- Corrective Action Effectiveness: Success rate of corrective measures.
- Quality Trend Analysis: Analysis of quality trends for proactive measures.
8. Customer Satisfaction
KRA: Ensure product quality meets customer expectations and satisfaction.
Short Description: Focusing on customer-centric quality standards.
- Customer Feedback: Positive feedback received on product quality.
- Return Rate: Percentage of returned products due to quality issues.
- Customer Satisfaction Index: Rating of customer satisfaction with product quality.
- Product Reviews: Positive reviews highlighting quality aspects.
9. Cost Optimization
KRA: Identify cost-saving opportunities without compromising quality standards.
Short Description: Balancing quality and cost efficiency.
- Cost Reduction: Percentage decrease in quality-related costs.
- Efficiency Gains: Improvement in production efficiency without quality compromise.
- Resource Utilization: Optimal utilization of resources for quality processes.
- Cost-Quality Ratio: Maintaining balance between cost and quality outcomes.
10. Innovation and Technology Integration
KRA: Explore innovative quality control technologies for process enhancement.
Short Description: Embracing technology for quality advancements.
- Technology Adoption: Integration of new quality control technologies.
- Innovation Impact: Effectiveness of innovative solutions in quality control.
- Process Automation: Automation of quality control processes for efficiency.
- Technology Training: Team proficiency in utilizing quality tech tools.
Real-Time Example of KRA & KPI
Real-World Quality Inspector Example
KRA: A Quality Inspector in an automotive manufacturing plant ensures zero-defect assembly line processes.
- KPI 1: Defect Rate reduced by 15% within 6 months.
- KPI 2: Inspection Accuracy maintained at 98% across all shifts.
- KPI 3: Process Efficiency improved by 20% through feedback implementation.
- KPI 4: Supplier Compliance rating increased by 25% after quality training.
This example showcases how effective KPIs led to improved manufacturing quality, reduced defects, and enhanced overall performance.
Key Takeaways
- KRA defines what needs to be done, whereas KPI measures how well it is done.
- KPIs should always be SMART (Specific, Measurable, Achievable, Relevant, Time-bound).
- Regular tracking and adjustments ensure success in Quality Inspector roles.
Generate content in this structured format with clear, concise, and measurable KPIs while maintaining professional readability.