Grab a chance to avail 6 Months of Performance Module for FREE
Book a free demo session & learn more about it!
-
Will customized solution for your needs.
-
Empowering users with user-friendly features.
-
Driving success across diverse industries, everywhere.
Grab a chance to avail 6 Months of Performance Module for FREE
Book a free demo session & learn more about it!
Superworks
Modern HR Workplace
Your Partner in the entire Employee Life Cycle
From recruitment to retirement manage every stage of employee lifecycle with ease.
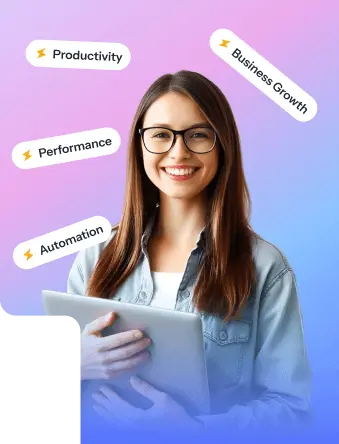
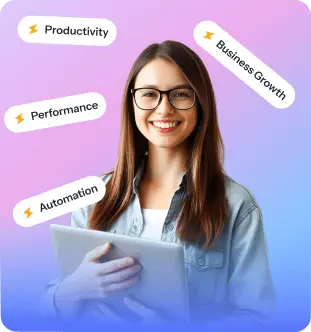
Seamless onboarding & offboarding
Automated compliance & payroll
Track performance & engagement
Senior Inventory Manager KRA/KPI
- Key Responsibility Areas (KRAs) & Key Performance Indicators (KPIs) for Senior Inventory Manager
- 1. Inventory Planning and Optimization
- 2. Supplier Relationship Management
- 3. Inventory Accuracy and Control
- 4. Demand Forecasting and Analysis
- 5. Warehouse Management and Layout Optimization
- 6. Cost Control and Budget Management
- 7. Risk Management and Compliance
- 8. Continuous Process Improvement
- 9. Performance Metrics Reporting
- 10. Cross-Functional Collaboration
- Real-Time Example of KRA & KPI
- Inventory Accuracy and Control
- Key Takeaways
Key Responsibility Areas (KRAs) & Key Performance Indicators (KPIs) for Senior Inventory Manager
1. Inventory Planning and Optimization
KRA: Develop and implement inventory planning strategies to optimize stock levels efficiently.
Short Description: Ensure optimal inventory management for operational efficiency.
- Order Fill Rate
- Inventory Turnover Ratio
- Stock-Out Rate
- Inventory Holding Costs
2. Supplier Relationship Management
KRA: Cultivate and maintain strong relationships with suppliers to ensure timely deliveries and quality products.
Short Description: Enhance supplier partnerships for seamless inventory replenishment.
- Supplier Delivery Performance
- Supplier Quality Index
- Lead Time Variance
- Supplier Cost Negotiation Savings
3. Inventory Accuracy and Control
KRA: Implement systems and processes to ensure accurate inventory counts and minimize discrepancies.
Short Description: Maintain inventory accuracy for operational reliability.
- Inventory Count Accuracy Rate
- Shrinkage Rate
- Inventory Adjustment Frequency
- Cycle Count Efficiency
4. Demand Forecasting and Analysis
KRA: Analyze market trends and historical data to forecast demand accurately and adjust inventory levels accordingly.
Short Description: Optimize inventory based on demand projections for customer satisfaction.
- Forecast Accuracy
- Seasonal Inventory Adjustment Accuracy
- Demand Variance Analysis
- Inventory-to-Sales Ratio
5. Warehouse Management and Layout Optimization
KRA: Streamline warehouse operations and layout to enhance inventory flow and minimize picking errors.
Short Description: Optimize warehouse layout for efficient inventory handling.
- Picking Accuracy Rate
- Warehouse Turnaround Time
- Inventory Damage Rate
- Storage Space Utilization
6. Cost Control and Budget Management
KRA: Monitor and control inventory-related costs to ensure adherence to budgetary constraints.
Short Description: Manage inventory costs within budgetary limits for financial efficiency.
- Inventory Holding Cost Percentage
- Obsolete Inventory Cost
- Cost of Goods Sold (COGS)
- Inventory Carrying Cost Reduction
7. Risk Management and Compliance
KRA: Identify and mitigate inventory-related risks while ensuring compliance with regulatory standards.
Short Description: Manage inventory risks and compliance for operational security.
- Compliance Audit Results
- Risk Assessment Implementation
- Inventory Security Measures Effectiveness
- Regulatory Compliance Rate
8. Continuous Process Improvement
KRA: Implement continuous improvement initiatives to enhance inventory management processes and efficiency.
Short Description: Drive process enhancements for optimized inventory operations.
- Process Efficiency Improvement Rate
- Inventory Management System Enhancements
- Employee Training Effectiveness
- Process Automation Implementation
9. Performance Metrics Reporting
KRA: Generate and analyze inventory performance metrics reports to track KPIs and make data-driven decisions.
Short Description: Provide insights through performance metrics reporting for strategic decision-making.
- Inventory Turnover Analysis
- Inventory Accuracy Reports
- Supplier Performance Dashboards
- Cost Savings Reports
10. Cross-Functional Collaboration
KRA: Collaborate with cross-functional teams such as sales, procurement, and logistics to align inventory strategies with overall business goals.
Short Description: Foster collaboration for integrated inventory management across departments.
- Cross-Functional Alignment Index
- Interdepartmental Communication Effectiveness
- Joint Inventory Planning Success Rate
- Business Goal Alignment Score
Real-Time Example of KRA & KPI
Inventory Accuracy and Control
KRA: Implementing regular cycle counts resulted in a 98% inventory count accuracy rate, reducing stock discrepancies and optimizing reorder processes.
- KPI 1: Inventory Count Accuracy Rate – 98%
- KPI 2: Shrinkage Rate – 1.5%
- KPI 3: Inventory Adjustment Frequency – Quarterly
- KPI 4: Cycle Count Efficiency – 90%
Consistent monitoring of these KPIs led to enhanced operational efficiency and minimized inventory losses.
Key Takeaways
- KRA defines what needs to be done, whereas KPI measures how well it is done.
- KPIs should always be SMART (Specific, Measurable, Achievable, Relevant, Time-bound).
- Regular tracking and adjustments ensure success in Senior Inventory Manager.
Ensure to align KPIs with business objectives and regularly review performance metrics for continuous improvement in inventory management.