Grab a chance to avail 6 Months of Performance Module for FREE
Book a free demo session & learn more about it!
-
Will customized solution for your needs.
-
Empowering users with user-friendly features.
-
Driving success across diverse industries, everywhere.
Grab a chance to avail 6 Months of Performance Module for FREE
Book a free demo session & learn more about it!
Superworks
Modern HR Workplace
Your Partner in the entire Employee Life Cycle
From recruitment to retirement manage every stage of employee lifecycle with ease.
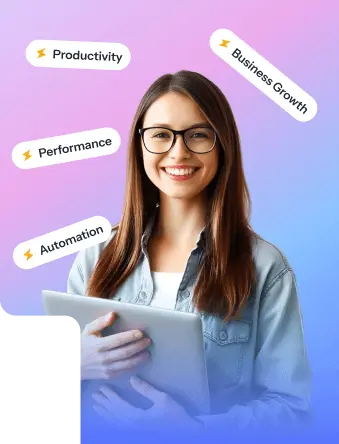
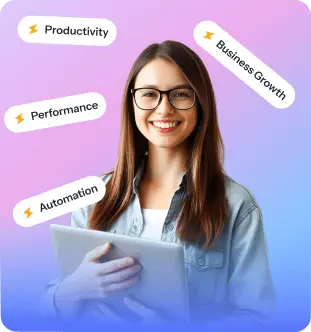
Seamless onboarding & offboarding
Automated compliance & payroll
Track performance & engagement
Senior Quality Engineer KRA/KPI
- Key Responsibility Areas (KRA) & Key Performance Indicators (KPI) for Senior Quality Engineer
- 1. Quality Management Systems
- 2. Process Improvement
- 3. Quality Assurance
- 4. Data Analysis and Reporting
- 5. Supplier Quality Management
- 6. Training and Development
- 7. Regulatory Compliance
- 8. Customer Experience Management
- 9. Risk Management
- 10. Team Leadership and Collaboration
- Real-Time Example of KRA & KPI
- Supplier Quality Management Example:
- Key Takeaways
Key Responsibility Areas (KRA) & Key Performance Indicators (KPI) for Senior Quality Engineer
1. Quality Management Systems
KRA: Ensure compliance and effectiveness of quality management systems.
Short Description: Oversight of QMS implementation and maintenance.
- Number of non-conformities identified
- Percentage of successful QMS audits
- Time taken to resolve major QMS issues
- Customer satisfaction ratings related to QMS
2. Process Improvement
KRA: Drive continuous improvement initiatives across processes.
Short Description: Enhance operational efficiency and quality standards.
- Percentage increase in process efficiency
- Number of successful process improvement projects completed
- Reduction in process errors or defects
- Employee engagement in process improvement activities
3. Quality Assurance
KRA: Develop and implement quality assurance strategies.
Short Description: Ensure products meet quality standards and specifications.
- Defect density rate in products/services
- Adherence to quality checkpoints and standards
- Number of customer complaints related to quality
- Percentage of products/services meeting quality criteria
4. Data Analysis and Reporting
KRA: Analyze quality data and generate insightful reports.
Short Description: Utilize data for informed decision-making.
- Accuracy and timeliness of quality reports
- Identification of key quality trends and patterns
- Utilization of data for process improvements
- Feedback on the relevance of quality reports
5. Supplier Quality Management
KRA: Monitor and enhance supplier quality performance.
Short Description: Ensure suppliers meet quality requirements.
- Supplier defect rate and improvement trends
- Timeliness of supplier corrective actions
- Supplier audit ratings and compliance levels
- Number of supplier-related quality incidents
6. Training and Development
KRA: Provide training on quality principles and practices.
Short Description: Enhance quality competencies within the team.
- Training participation rates and feedback
- Improvement in quality-related skills and knowledge
- Application of training outcomes in quality processes
- Employee certification/accreditation in quality disciplines
7. Regulatory Compliance
KRA: Ensure adherence to relevant quality regulations and standards.
Short Description: Mitigate risks associated with non-compliance.
- Number of compliance audits passed
- Timely implementation of regulatory updates
- Resolution of compliance issues within deadlines
- Incidents of non-compliance and corrective actions taken
8. Customer Experience Management
KRA: Enhance customer satisfaction through quality initiatives.
Short Description: Improve overall customer experience and loyalty.
- Customer satisfaction scores and feedback trends
- Resolution time for customer quality concerns
- Number of repeat customer complaints
- Implementation of customer-centric quality improvements
9. Risk Management
KRA: Identify and mitigate quality-related risks.
Short Description: Safeguard against quality failures and liabilities.
- Risk assessment completion and action plans implemented
- Incidents of quality-related risks identified and resolved
- Effectiveness of risk mitigation strategies
- Reduction in quality risk exposure over time
10. Team Leadership and Collaboration
KRA: Provide leadership and foster a culture of quality excellence.
Short Description: Promote teamwork and quality mindset within the organization.
- Team performance in quality-related projects
- Employee satisfaction and engagement levels
- Recognition for quality achievements and contributions
- Collaboration with cross-functional teams for quality goals
Real-Time Example of KRA & KPI
Supplier Quality Management Example:
KRA: Monitoring supplier defect rates to ensure high-quality materials for production.
- KPI 1: Quarterly Supplier Defect Rate (%)
- KPI 2: Timeliness of Supplier Corrective Actions (days)
- KPI 3: Supplier Audit Ratings (score out of 100)
- KPI 4: Number of Supplier Quality Incidents per Quarter
This example showcases how tracking supplier quality metrics led to improved product quality, reduced defects, and strengthened supplier relationships.
Key Takeaways
- KRA defines what needs to be done, whereas KPI measures how well it is done.
- KPIs should always be SMART (Specific, Measurable, Achievable, Relevant, Time-bound).
- Regular tracking and adjustments ensure success in Senior Quality Engineer role.