Grab a chance to avail 6 Months of Performance Module for FREE
Book a free demo session & learn more about it!
-
Will customized solution for your needs
-
Empowering users with user-friendly features
-
Driving success across diverse industries, everywhere.
Grab a chance to avail 6 Months of Performance Module for FREE
Book a free demo session & learn more about it!
Superworks
Modern HR Workplace
Your Partner in the entire Employee Life Cycle
From recruitment to retirement manage every stage of employee lifecycle with ease.
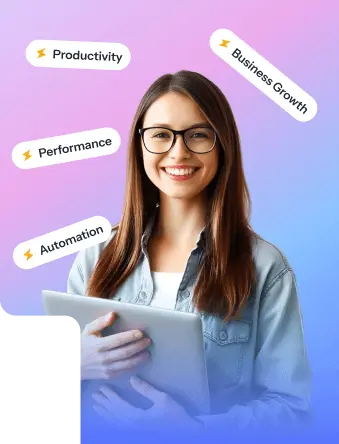
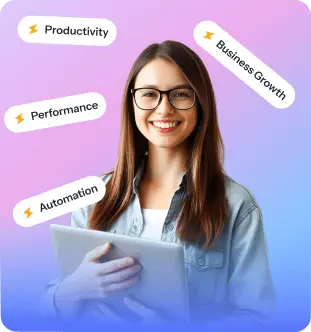
Seamless onboarding & offboarding
Automated compliance & payroll
Track performance & engagement
Of Technician Maintenance KRA/KPI
- Job Description
- Key Responsibility Areas (KRA) & Key Performance Indicators (KPI)
- 1. Equipment Maintenance
- 2. Safety Compliance
- 3. Inventory Management
- 4. Performance Monitoring
- 5. Training and Development
- 6. Documentation and Reporting
- 7. Cost Management
- 8. Customer Satisfaction
- 9. Team Collaboration
- 10. Continuous Improvement
- Real-Time Example of KRA & KPI
- Reducing Downtime through Preventive Maintenance
- Key Takeaways
Job Description
As a Technician Maintenance, your role involves ensuring the proper functioning and upkeep of equipment and machinery within an organization. You will be responsible for conducting routine maintenance, troubleshooting issues, and performing repairs to minimize downtime and maximize operational efficiency.
Key Responsibility Areas (KRA) & Key Performance Indicators (KPI)
1. Equipment Maintenance
KRA: Ensure the regular maintenance and servicing of all equipment to prevent breakdowns.
Short Description: Maintain equipment to ensure optimal performance.
- Percentage of scheduled maintenance completed on time
- Downtime percentage due to equipment failures
- Average time taken to resolve equipment issues
- Percentage reduction in maintenance costs
2. Safety Compliance
KRA: Adhere to safety protocols and regulations to create a secure work environment.
Short Description: Ensure compliance with safety standards.
- Number of safety inspections conducted
- Incident rate per month
- Completion rate of safety training for technicians
- Percentage decrease in safety violations
3. Inventory Management
KRA: Manage spare parts inventory efficiently to support maintenance activities.
Short Description: Optimize spare parts inventory for timely repairs.
- Inventory turnover rate
- Percentage of critical spare parts availability
- Percentage of obsolete parts identified and removed
- Cost savings through effective inventory management
4. Performance Monitoring
KRA: Monitor equipment performance and identify areas for improvement.
Short Description: Analyze equipment performance for enhancements.
- Percentage increase in equipment uptime
- Number of performance improvement initiatives implemented
- Energy efficiency improvements achieved
- Reduction in recurring equipment issues
5. Training and Development
KRA: Continuously enhance skills and knowledge through training programs.
Short Description: Develop technician skills for better performance.
- Training hours completed per technician
- Skills improvement assessment results
- Number of certifications obtained by technicians
- Application of new skills in maintenance tasks
6. Documentation and Reporting
KRA: Maintain accurate maintenance records and generate performance reports.
Short Description: Document maintenance activities and analyze data.
- Accuracy of maintenance logs and reports
- Timeliness of report submissions
- Number of insights derived from maintenance data analysis
- Improvements based on maintenance reports
7. Cost Management
KRA: Control maintenance costs while ensuring quality service delivery.
Short Description: Optimize maintenance expenditures without compromising quality.
- Percentage variance between actual and budgeted maintenance costs
- Cost per maintenance activity trend analysis
- Cost savings initiatives implemented
- Return on investment for maintenance expenditures
8. Customer Satisfaction
KRA: Meet customer expectations by providing timely and effective maintenance solutions.
Short Description: Ensure customer satisfaction through maintenance services.
- Customer feedback ratings on maintenance services
- Resolution time for customer-reported issues
- Repeat service request rate
- Customer retention rate post-maintenance service
9. Team Collaboration
KRA: Collaborate effectively with other teams to enhance overall operational efficiency.
Short Description: Foster teamwork for seamless maintenance operations.
- Number of cross-functional projects participated in
- Team communication effectiveness score
- Feedback from other departments on maintenance support
- Joint initiatives resulting in improved processes
10. Continuous Improvement
KRA: Identify opportunities for process optimization and implement continuous improvement initiatives.
Short Description: Drive ongoing enhancements in maintenance practices.
- Number of improvement suggestions implemented
- Reduction in maintenance response time due to improvements
- Percentage increase in efficiency post-improvement projects
- Quality improvement metrics in maintenance processes
Real-Time Example of KRA & KPI
Reducing Downtime through Preventive Maintenance
KRA: By implementing a preventive maintenance program, the organization reduced machine downtime by 20% within six months.
- KPI 1: Percentage decrease in unplanned downtime
- KPI 2: Number of preventive maintenance tasks completed per month
- KPI 3: Increase in equipment reliability index post-implementation
- KPI 4: Cost savings achieved through reduced downtime
This example showcases how focusing on preventive maintenance as a KRA led to tangible improvements in operational efficiency and cost savings.
Key Takeaways
- KRA defines what needs to be done, whereas KPI measures how well it is done.
- KPIs should always be SMART (Specific, Measurable, Achievable, Relevant, Time-bound).
- Regular tracking and adjustments ensure success in Technician Maintenance.
Ensure the content is structured, informative, and tailored for SEO optimization to effectively communicate the responsibilities and performance indicators for a Technician Maintenance role.