Downtime refers to any period when machines, equipment, or systems are non-operational, leading to lost production time and decreased operational efficiency. It increases downtime costs, disrupts workflows, and negatively impacts customer expectations.
Grab a chance to avail 6 Months of Performance Module for FREE
Book a free demo session & learn more about it!
-
Will customized solution for your needs.
-
Empowering users with user-friendly features.
-
Driving success across diverse industries, everywhere.
Grab a chance to avail 6 Months of Performance Module for FREE
Book a free demo session & learn more about it!
Superworks
Modern HR Workplace
Your Partner in the entire Employee Life Cycle
From recruitment to retirement manage every stage of employee lifecycle with ease.
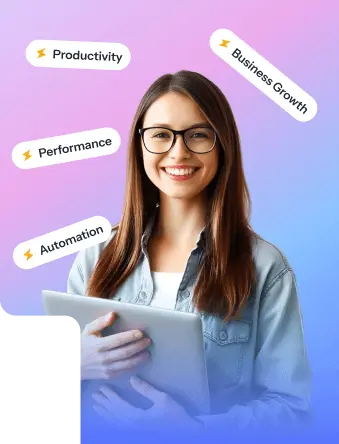
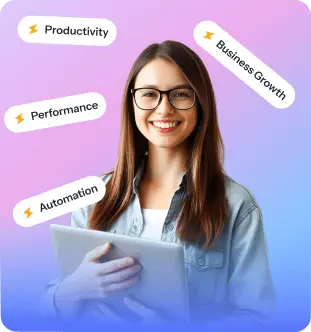
Seamless onboarding & offboarding
Automated compliance & payroll
Track performance & engagement
Reduce Downtime And Save Money: 4 Expert-Backed Strategies
- reduce downtime
- 11 min read
- April 10, 2025
Every minute of downtime can cost companies thousands and even lakhs. And it literally doesn’t matter whether it’s unplanned downtime due to some equipment failures or any planned downtime for regular maintenance, the time that has been lost will have a direct effect on productivity & revenue. So, about downtime events, here comes the real question, how to effectively reduce downtime & improve operational efficiency?
And this question [which is getting more & more common these days] can be asked by a regular employee or some HR, and even by the CEO. But the thing is, that most of the time, they fail to get a proper answer cum solution. Hence, today, we have come up with the answer, and that too with a detailed guide consisting of not only one but 4 expert-backed strategies.
So, read this guide, and learn the expert-backed strategies to help you easily reduce downtime, minimize costs & optimize operations. So, whether you’re managing a manufacturing plant, leading a maintenance team, or overseeing field operations, these are the strategies that will keep helping you with employee tracking, downtime tracking, predicting failures & maximizing uptime.
So, let’s start with the basics of how to reduce downtime in production and other various sectors before directly starting to dive into the very strategies.
- How to Reduce Downtime?
- 4 Strategies to Reduce Downtime
- Strategy 1: Implement Preventive Maintenance Plans
- Strategy 2: Leverage Predictive Maintenance Technology
- Strategy 3: Streamline Workflows with Field Force Management
- Strategy 4: Train and Empower Your Workforce
- Best Tool to Reduce Downtime
- Parting Thoughts,
How to Reduce Downtime?
Before we can start literally minimizing the downtime in your field operations, we should be clear with “What is Downtime?”
Basically, downtime refers to any period when some equipment, machines, or even systems are not operational enough. And keep leading companies to production loss and reduced overall equipment effectiveness. Furthermore, there are two types of downtime events:
- Planned Downtime – Planned downtime includes scheduled maintenance, system upgrades, and part replacement so that failures can be prevented.
- Unplanned Downtime – In this section of unplanned downtime, there comes some unexpected breakdowns, system downtime, and even performance issues- which can lead to lost production time.
Why Is Reducing Downtime Critical?
Downtime always increases the operational cost, because of which the team could end up reducing productivity, and it will keep impacting customer expectations negatively. Furthermore, manufacturing plants, field operations & IT systems just have to take a much more proactive approach to minimize disruptions.
Ways to Reduce Downtime
- Implement preventive maintenance and predictive maintenance.
- Use real-time monitoring to detect performance issues before failures occur.
- Optimize spare parts inventory to avoid delays in part replacement.
- Use automated systems to streamline maintenance and reduce manual errors.
- You should train your maintenance team to troubleshoot issues faster.
Once the team starts to follow these strategies, they can reduce their unplanned downtime, improve equipment effectiveness & enhance continuous improvement efforts.
4 Strategies to Reduce Downtime
Reducing downtime really requires a mix of proactive planning, smart technology & a well-trained maintenance team. Hence, all the businesses that rely on heavy equipment, manufacturing processes, or field operations will have to address downtime incidents way before they can cause lost productivity & costly delays.
The 4 expert-backed strategies below will help you focus on both preventive & predictive approaches to ensure that all of your machines, systems, and teams are always prepared. From automated systems to better employee tracking, these expert strategies will keep helping you reduce your unplanned downtime, minimize equipment failures & optimize production efficiency.
Let’s explore each and every strategy in detail, starting from preventive maintenance plans.
Strategy 1: Implement Preventive Maintenance Plans
One of the most effective ways to answer the question of “How to minimise downtime” is going through preventive maintenance. Instead of waiting for machine downtime to happen, businesses really should take a proactive approach by scheduling their maintenance regularly to prevent breakdowns.
What Is Preventive Maintenance?
Preventive maintenance refers to scheduled inspections, servicing & even the repairs designed to prevent equipment failures even way before they happen. This can easily help companies learn “How to reduce downtime and increase productivity,” this way they can extend the life of their machines & avoid costly emergency repairs.
How Preventive Maintenance Reduces Downtime?
- Identifies Issues Before They Escalate – Regular checks can help teams detect all the small problems even before they can cause system downtime.
- Reduces Unplanned Downtime – Instead of consistently dealing with unexpected downtime incidents, planned servicing can help teams keep their operations running smoothly.
- Improves Equipment Effectiveness – Proper maintenance all the time can easily ensure machines perform at their best, and help reduce the chances of performance issues.
- Low Downtime Costs – Scheduled maintenance is literally much less costly than all the sudden breakdowns that can halt production.
- Enhances Operational Efficiency – Keeping machines in their prime conditions keeps improving overall production performance.
Best Practices for Preventive Maintenance
- Create a Maintenance Schedule – Companies can use field force management software or automated systems to track their maintenance dates seamlessly.
- Use Real-Time Monitoring – Technology like vibration analysis can help companies detect performance issues way before failure can happen.
- Keep Spare Parts Ready – A well-managed spare parts inventory is always there to prevent delays in part replacement.
- Train the Maintenance Team – A well-trained team can easily fix all the minor problems way before they can cause a loss in production time.
- Track Downtime Data – Use downtime analysis to easily identify recurring issues & improve continuous improvement efforts.
By implementing preventive maintenance, companies can quite effectively minimize downtime, enhance operational efficiency & keep production running smoothly.
Strategy 2: Leverage Predictive Maintenance Technology
While preventive maintenance can help teams reduce their downtime incidents, it operates on a fixed schedule. Predictive maintenance, on the other hand, keeps utilizing real-time monitoring & machine learning to predict when equipment failures might happen in the future. This kind of approach keeps allowing businesses to reduce their unplanned downtime by servicing equipment only when necessary.
What Is Predictive Maintenance?
Predictive maintenance utilizes data analytics, artificial intelligence & sensor-based tracking quite easily to detect signs of wear & tear in machines. Instead of waiting for a scheduled check-up, the system alerts the maintenance team whenever a machine is likely to fail, allowing for timely intervention.
How Predictive Maintenance Reduces Downtime
- Reduces Machine Downtime – Since maintenance is performed only when it’s required, it keeps preventing unnecessary system downtime.
- Optimizes Spare Parts Usage – Data-driven insights keep helping teams determine when a part replacement is quite necessary, which directly can reduce waste and cut costs.
- Enhances Downtime Reduction Strategies – With the help of Downtime Analysis, companies can easily refine their approach over time.
Best Practices for Implementing Predictive Maintenance
- Install IoT Sensors – These devices keep providing all the real-time data on machine health, helping identify potential failures early.
- Use Vibration Analysis – Monitoring vibrations can easily help detect wear & tear before it leads to machine downtime.
- Adopt AI-Driven Maintenance Tools – Artificial intelligence can easily analyze patterns in downtime events by suggesting solutions.
- Track Downtime Trends – Analyzing historical downtime reasons helps predict and prevent future breakdowns.
- Train the Maintenance Team – Employees should know how to interpret predictive maintenance alerts and act on them quickly.
Businesses that keep integrating predictive maintenance technology into their manufacturing process or field operations can easily minimize their downtime, cut costs & ensure smooth production.
Strategy 3: Streamline Workflows with Field Force Management
A well-structured workflow can easily reduce a company’s downtime by efficiently improving its communication, coordination & task execution. Hence, companies should use Field Force Management (FFM) software, because it can help businesses track downtime, optimize team performance & reduce unplanned stops by ensuring that maintenance & operational teams are well-aligned.
How FFM Helps Reduce Downtime?
- Automates Task Scheduling – With this solution, companies can easily reduce their unplanned downtime, because it can ensure that maintenance tasks are assigned & completed on time.
- Improves Response Time Tracking – When downtime events happen, proper field force management continues to help dispatch the right personnel at once.
- Enhances Employee Tracking – This solution keeps ensuring the right team members are always available for urgent repairs.
- Reduces Downtime Costs – Optimized workflows are there to prevent delays, to help lower downtime costs, and to improve the company’s operational efficiency.
Best Practices for Using FFM to Reduce Downtime
- Adopt Automated Systems – Utilize field force management tools to create automated maintenance workflows, and reduce their system downtime.
- Monitor Equipment Effectiveness – Track machine performance & all the equipment downtime to easily identify all the problematic areas.
- Improve Communication Between Teams – A centralized system allows seamless coordination between the company’s maintenance team & operators.
- Use Data for Continuous Improvement – Field force management provides detailed insights into downtime reasons, which directly allows businesses to refine their maintenance strategies seamlessly.
- Enhance Customer Expectations – Reducing delays in such field operations can efficiently lead to better service delivery.
By optimizing workflows with FFM, all the businesses in the world can effectively reduce their downtime, enhance productivity & minimize costly disruptions in field operations and manufacturing.
Strategy 4: Train and Empower Your Workforce
Even with the best technology & maintenance systems, a poorly trained workforce
can lead to frequent downtime incidents. Ensuring that employees understand how to reduce downtime and properly handle equipment is essential for maintaining operational efficiency and reducing lost productivity.
How Workforce Training Reduces Downtime?
- Reduces Human Errors – Well-trained employees are less likely to cause equipment failures compared to new ones, and the reason we can consider is improper handling.
- Improves Maintenance Response Time – A skilled maintenance team can sufficiently fix issues faster than the newbies, and that can help businesses reduce lost production time.
- Enhances Predictive & Preventive Maintenance Implementation – Workers who really understand the meaning of predictive maintenance can easily take action before failures occur.
- Minimizes System Downtime – Employees who are trained in troubleshooting can easily resolve minor performance issues and that too without waiting for expert intervention.
- Boosts Overall Equipment Effectiveness – Proper training can easily lead to better equipment effectiveness & less production loss.
Best Practices for Workforce Training to Reduce Downtime
- Implement Regular Training Programs – Schedule ongoing training sessions to keep employees updated on the latest maintenance best practices.
- Use Digital SOPs & Employee Tracking – Provide step-by-step guides to help workers handle equipment downtime effectively.
- Simulate Downtime Scenarios – Train teams on how to respond to unplanned downtime quickly and efficiently.
- Encourage a Proactive Approach – Teach employees to identify downtime reasons and report potential failures before they escalate.
- Leverage Field Force Management Software – Use digital tools to track training progress and ensure compliance with standard procedures.
By training and empowering the workforce, businesses can significantly reduce unplanned downtime, enhance response time, and increase production efficiency.
Still, struggling with equipment failures now & then?
Get the best solution for your business now!
Best Tool to Reduce Downtime
The most practically effective way to reduce their downtime is simply by using Field Force Management software. Furthermore, this efficient tool integrates predictive maintenance, preventive maintenance, real-time monitoring & inventory tracking all into one single platform. And with the help of this integration, it keeps ensuring that all machines, teams & processes are working in sync to minimize both downtime & boost operational efficiency.
Why Choose FFM Software?
- Automates Maintenance Scheduling – This scheduling helps reduce all unplanned downtime by ensuring timely maintenance regularly.
- Real Time Monitoring – This prior monitoring helps track machine performance & detect all potential issues even before they escalate.
- Spare Parts Inventory Management – Helps companies prevent their equipment downtime due to missing parts.
- Downtime Analysis & Reporting – Identifies downtime reasons priorly by providing insights for continuous improvement.
- Optimizes Workforce Efficiency – Improves response time tracking & always assigns the right team members for quick fixes.
The Right FFM Software Saves Money & Increases Productivity
By choosing the best FFM tool like Superworks’ field force management software, businesses can effectively;
- Reduce their downtime,
- Prevent costly production losses, and
- Enhance overall equipment effectiveness.
Hence, you should always invest in the right technology, like Superworks, because that is what actually means fewer interruptions, lower downtime costs & much smoother operations.
Parting Thoughts,
Downtime is expensive but for obvious reasons is preventable. So, whether it’s due to unplanned stops, equipment failures, or some inefficient workflows, businesses that fail to address it will be always prone to reduced employee productivity, and high costs. So, whenever the companies want to reduce downtime and increase efficiency, they can start implementing;
- Preventive maintenance,
- Predictive maintenance,
- Optimized workflows,
- Workforce training, and
- Inventory management
And companies can simply do that once if they choose to invest in the right field force management software. Because software of such kind can help them ensure sustainable operations management, and ensure that teams, machines & systems are working in sync to prevent all the costly disruptions.
By concluding this blog about reducing downtime, we want to tell you about one thing, and that is “taking a proactive approach to downtime reduction isn’t just about saving money!” – Rather it’s about creating quite a sustainable, high-performance business that always meets customer expectations & operates at peak efficiency.
FAQs
What is downtime, and why is it costly?
How can businesses effectively reduce downtime?
Businesses can reduce downtime by:
- Implementing preventive and predictive maintenance
- Using real-time monitoring to detect issues early
- Optimizing workflows and workforce training
- Managing spare parts inventory efficiently
- Leveraging Field Force Management (FFM) software for automation
What’s the difference between planned and unplanned downtime?
Planned Downtime – Scheduled maintenance, part replacement, or upgrades that improve long-term performance.
Unplanned Downtime – Unexpected equipment failures, system crashes, or production stops that lead to lost productivity and higher costs.
How does predictive maintenance help minimize downtime?
Predictive maintenance seamlessly utilizes machine learning, vibration analysis & real-time data tracking to detect potential failures before they occur. This allows businesses to reduce unplanned downtime by fixing issues before they escalate.
Why is spare parts management important for downtime reduction?
A lack of needed spare parts can cause so many delays in fixing equipment, which directly can lead to prolonged machine downtime. Hence, you should all have a well-managed inventory because it can prevent production loss & ensure quick part replacement whenever needed.